Quiet air cleaning solution from Extractly installed at Staverton (UK) Ltd
- PWT
- Jan 10
- 4 min read
Leading dust and fume extraction specialists, Extractly Limited, recently completed the installation and commissioning of new dust extraction and filtration plant for a major UK furniture manufacturer based in Rotherham, South Yorkshire.

Originating from the village of Staverton, South Devon, and with almost a century of history behind it, the Staverton brand has become synonymous with high-quality contemporary office furniture.
In the late 1920s, a team of craftsmen, including joiners and cabinetmakers, was recruited to undertake works on the Dartington Hall estate and, in 1931, Staverton Builders Ltd was incorporated. Over the decades, the business has ridden the storms of change but, throughout its various phases and guises, has continued to be design-led and, today, Staverton (UK) Ltd enjoys an enviable reputation as a responsible and reliable award-winning British manufacturer.
While Staverton’s showroom and sales team are based in the heart of London’s creative Clerkenwell district, its design, manufacturing and admin functions are accommodated in a strategically-located 38,000sq.ft facility, alongside the M18 motorway, on the outskirts of Rotherham.

In the busy workshop, responsibility for supervising and managing machining operations is the duty of Production Manager, Mark Powell. “When it comes to dust producing machines, we’ve got some big hitters here,” says Mark, who’s been with Staverton for just a quarter of a century. “There are three high-speed CNC machining centres that require around 15,000m3 of extraction an hour between them, plus a couple of big saws and an edgebander, which together, need about 10,000m3. On top of that we also have a snip saw, spindle moulders and BHX drilling centres, all of which can easily add another 5,000m3 per hour if they’re being used at the same time.”
A compelling proposal
Staverton’s previous main fan and filter unit were both nearing the end of their service life and, although the extraction system had been upgraded back in 2015 to take advantage of Ecogate® ‘on-demand’ energy-saving technology, the company’s additional investments over the years in newer, high-speed machinery meant that the system was now operating close to its maximum capacity. Extractly Ltd is also the Master UK Distributor and Installer for Ecogate® in the UK and, as a result of a timely customer relationship interaction with Staverton, Sales Director, Jake Oldfield, was invited to visit the Rotherham factory to survey the site and assess Staverton’s current extraction requirements.
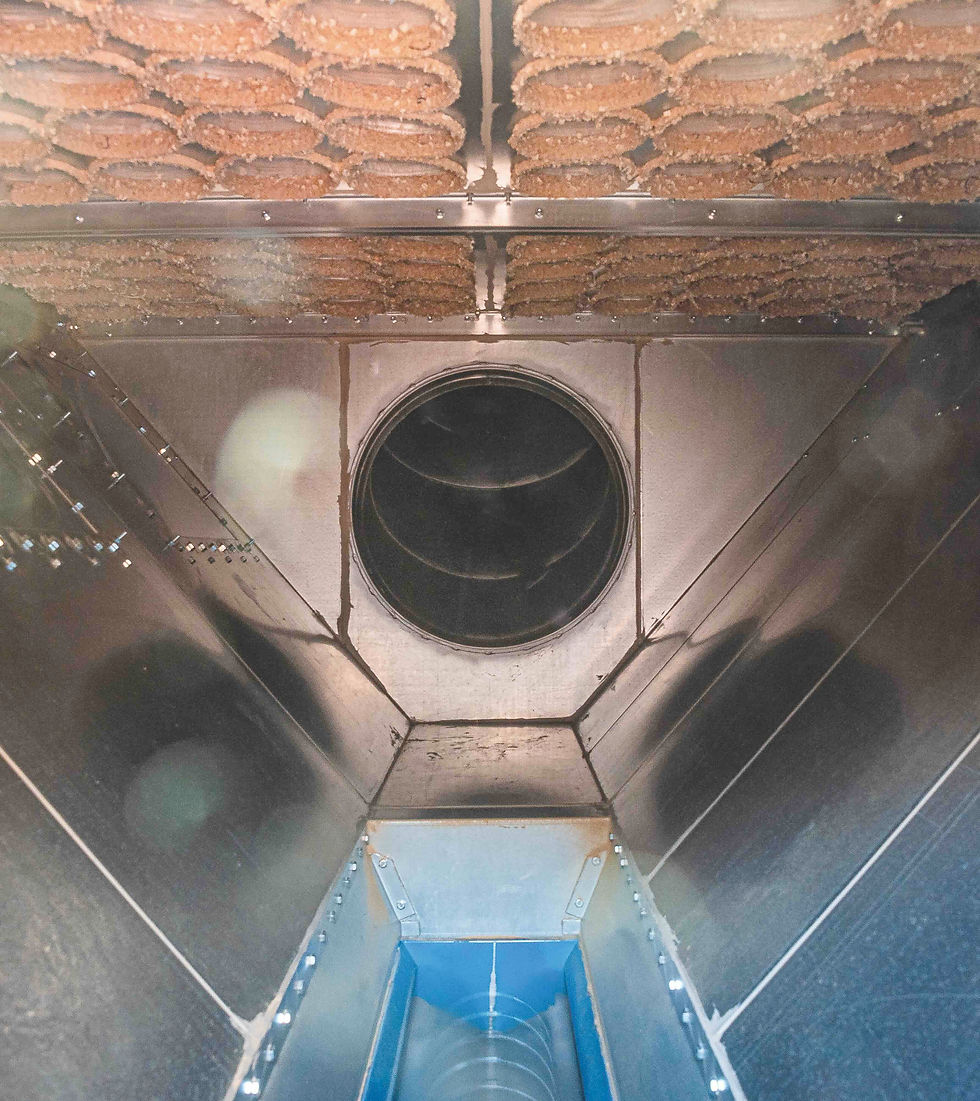
Jake explains: “Since Staverton already had Ecogate® technology installed across the factory, it was evident from recorded system data that the old filter unit and fan were being stretched to the limit and now clearly lacked the power required to efficiently extract dust and wood waste from all the machinery being used.” With the old fan and filter being rather long in the tooth, the only satisfactory solution was to install a modern, efficient replacement filter unit, with greater capacity, together with a more powerful main fan.
“Extractly put together a compelling proposal,” Mark added. “We previously had a 37kW fan, running flat out, but Jake recommended replacing this with a 55kW version, which would easily cope with today’s requirements, but also give us plenty of leeway for future expansion. Compared with our previous fan this is quite a step up in power but, with Ecogate® already installed, it means the fan only consumes the energy required to extract from machines that are operating at any point in time.”

Maximum extraction & efficiency
For dust collection and filtration, Extractly installed a new ATEX filter unit with sufficient capacity to filter 33,000m3 of dust-laden air every hour. “To achieve maximum extraction efficiency from the new system, we’ve installed the fan on the filter unit’s ‘clean’ side,” Jake explains, “and, since dust and wood waste doesn’t pass through the fan, a more efficient impeller design can be used. As a result, the fan consumes less electricity, and ongoing maintenance is minimised due to the inevitable reduction in wear and tear.”
Dust and wood waste is removed from the airflow as it’s drawn through an array of tubular filter bags, which in turn are cleaned by three 1.5kW regeneration fans. Collected waste is then removed, pressure-free, from the filter unit by means of a rotary valve before being blown by a 15kW ATEX transport fan into an adjacent storage container.

Of benefit to personnel working in the Staverton factory, as well as those in neighbouring businesses, the silencer – fitted by Extractly above the main fan – is very effective in keeping noise to a minimum. In addition – and to comply with ATEX regulations – Extractly installed an explosion isolation valve into the main ductwork, close to the filter unit. “We always recommend the inclusion of a non-return valve,” says Jake. “In the unlikely event of an explosion occurring in the filter unit, the valve prevents a pressure wave and flames travelling through the ductwork and into the factory.”
In conclusion, Mark confirmed: “The new extraction works really well – the advanced filter unit has made a significant difference to the efficiency of our waste collection, and to our delight, Extractly managed to complete the whole installation with minimal machine downtime.”
To find out more about Extractly Limited, call 01924 520 462, email info@extractly.co.uk or visit www.extractly.co.uk.